Solutions
Our custom-made systems seamlessly complement the core of various industries. See how the future is taking shape.
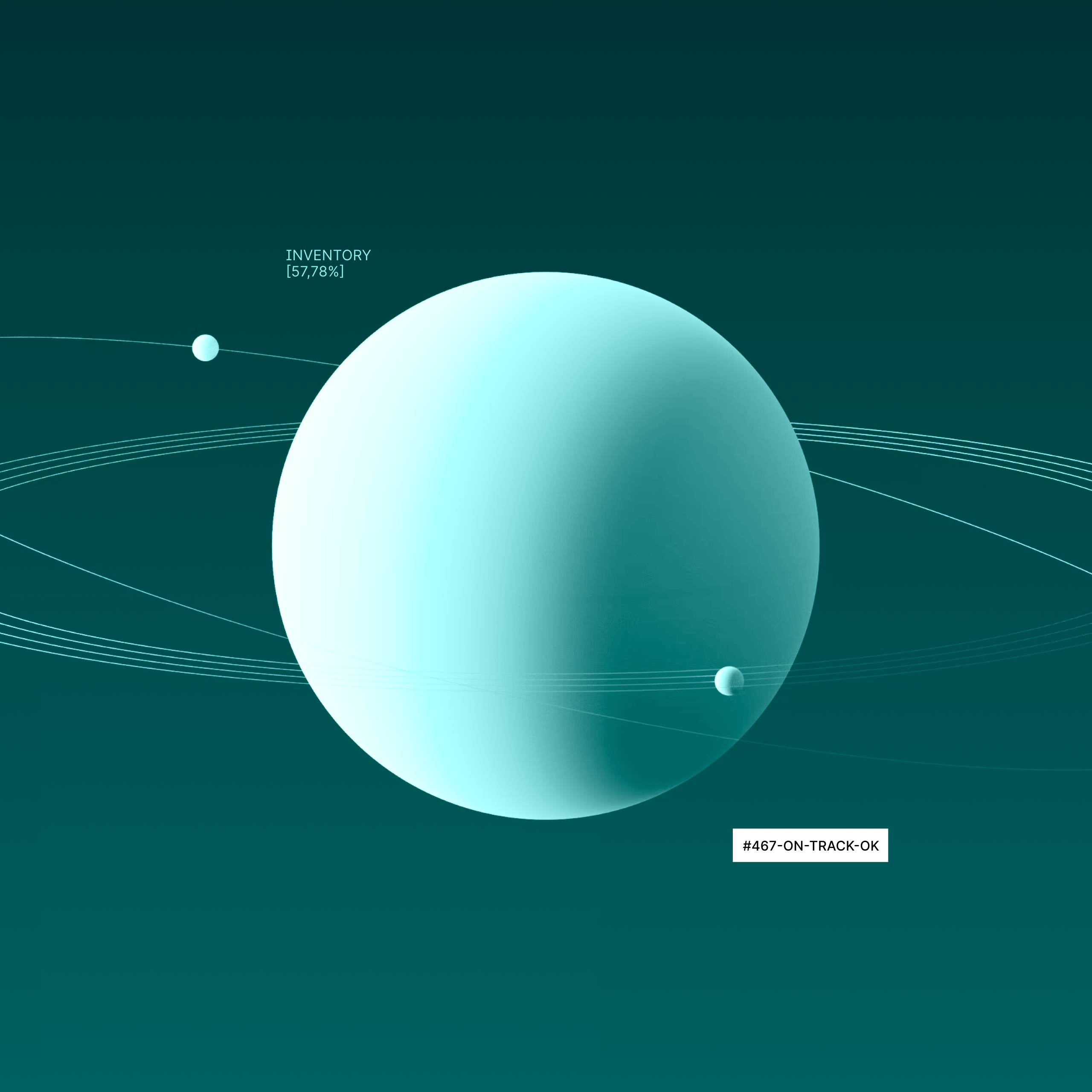
Effective Inventory
Optimization with MyIO
All-in-one inventory monitoring, demand forecasting, and predictive maintenance minimize risk and maximize profitability of your business.
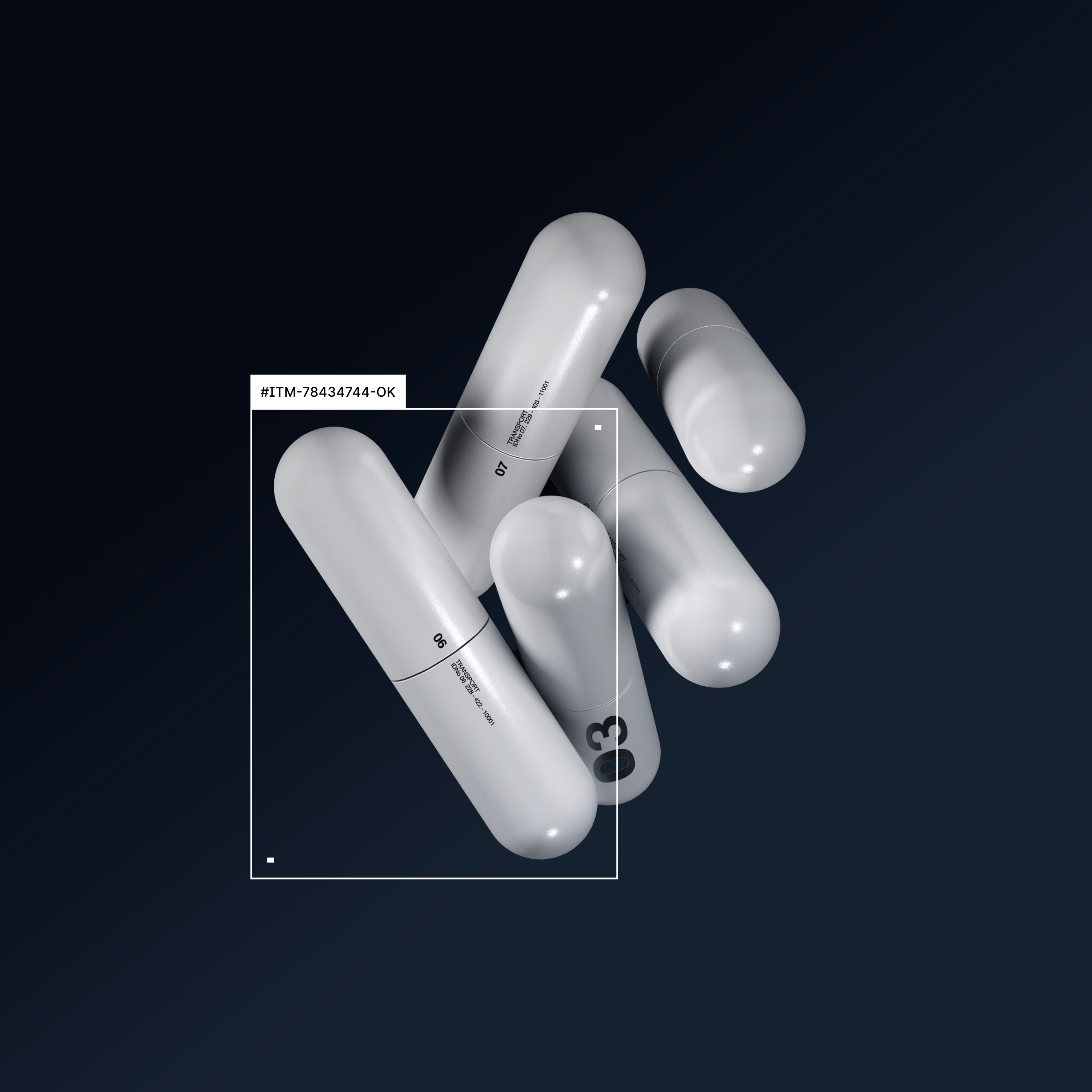
Quality Control
with Computer Vision
Image analysis technology based on deep learning helps gain valuable quality control insights that improve your production.
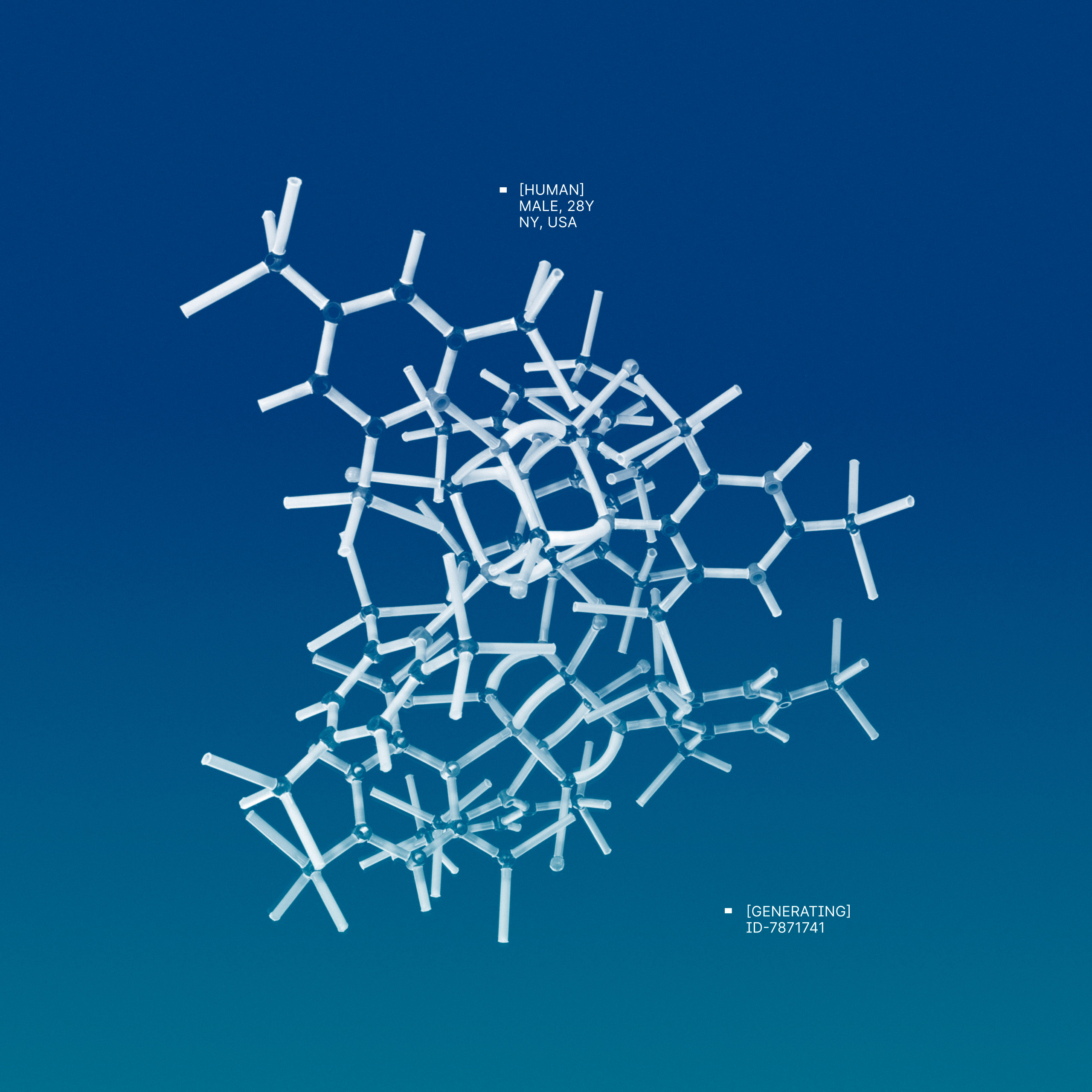
Ingenious Genomic Data
Processing with Floxgen
A cloud-ready platform for processing and analyzing genomic data saves bioinformaticians time and energy.

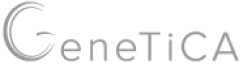

Natural Data Interpretation with Cognitive Assistant
Augmented human intelligence using large language models and other machine learning techniques to help you interpret and understand vast amounts of data.
A Case in Point
We bridge the gap between the latest AI research and real-world deployment. Explore in more detail.
A Breeding Ground
for Innovation
Cooperation is the best way to solve complex challenges. At DNAi, top architects, researchers, AI developers, mathematicians, and subject-matter experts share their knowledge to create groundbreaking solutions.
Unlock value growth that breaks through traditional limitations.
Amplify your team’s capabilities, creativity, productivity, and operational efficiency.
Stay ahead of the curve in a rapidly changing environment while preserving your uniqueness.
Support sustainable practices and ESG initiatives, setting a benchmark for responsible business.
Embrace your accountability and error identification through unbiased data insights.
Keep your customers satisfied and loyal with incredibly personalized experiences.
Create innovative value propositions and expand market opportunities.
Transform low profit into high growth in a competitive environment.
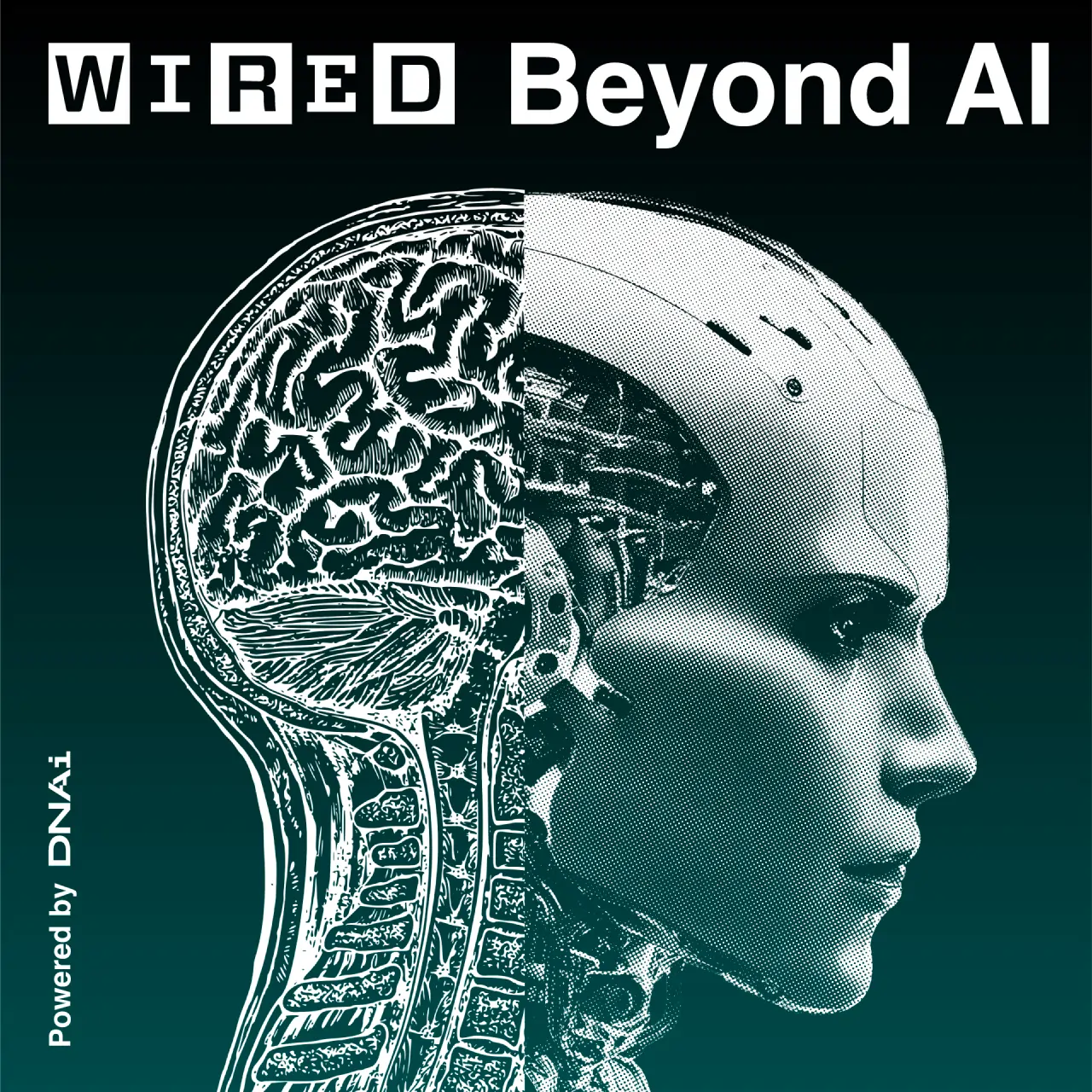
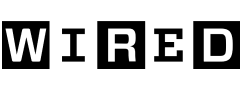
Beyond AI
The tireless search for the potential and limits of new technologies has connected us with Wired and top minds from around the world in a discussion that goes beyond the buzz.
DO What You Can Imagine
DO
What You
Can Imagine
An environment of freedom, responsibility, inclusive collaboration, and out-of-the-ordinary thinking. People with an open mind, who are not afraid of innovation, are willing to take risks, learn from each other and own mistakes, and deliver, will always find an opening with us.
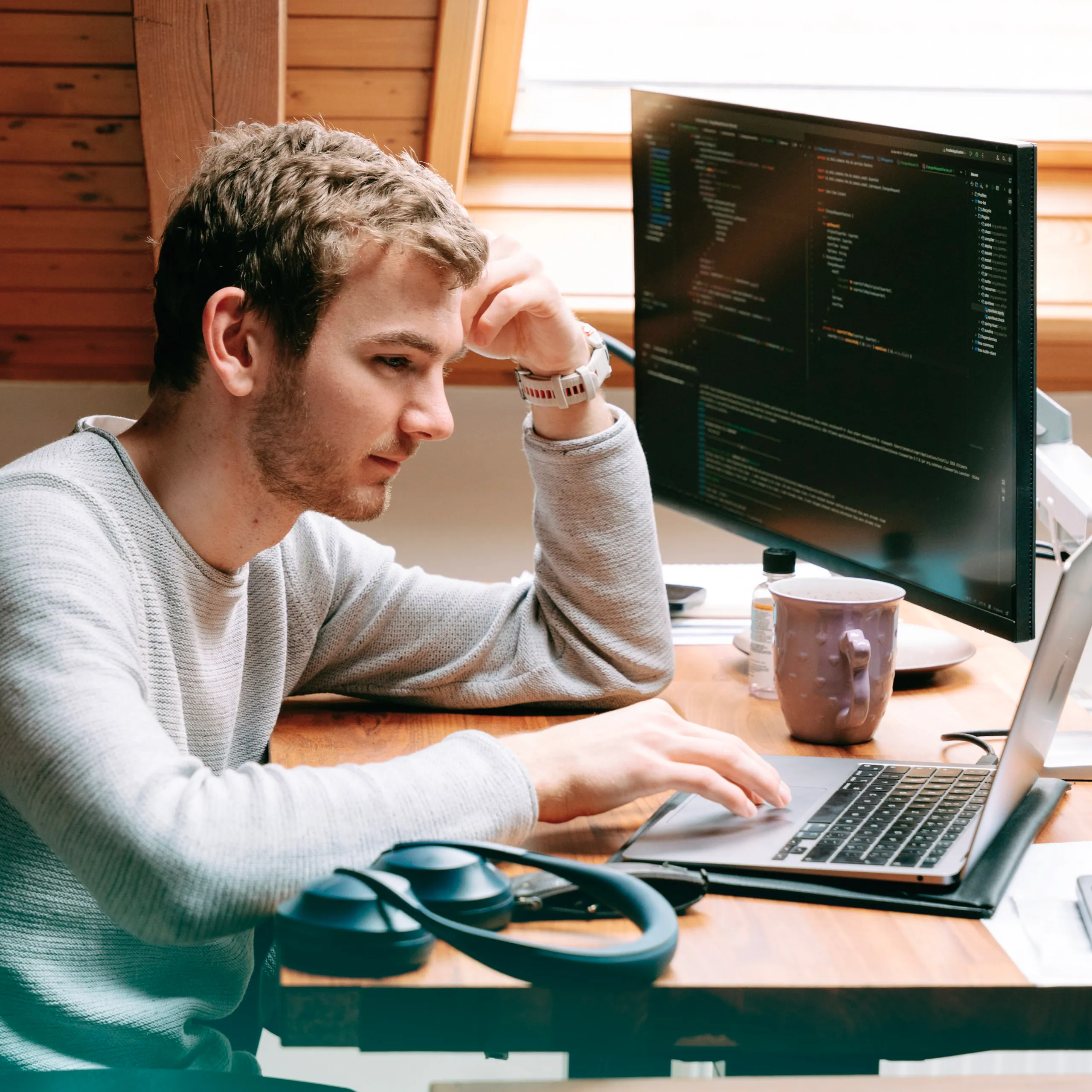
Keep in Touch
with Technological
Evolution
Curious how AI could enrich your industry DNA? Connect with us to meet our expertise.